
The wetting agents also referred as surfactants are very vital to minimize the surface tension arising between two types of liquid. They also find their utility in the reduction of tension existing between a liquid and a solid material. The wetting agents also double up as emulsifiers and water infiltration agents depending upon the requirement.
Raj Specialty additives continue to gladden hearts with their wide range of offering of additives and it is an absolute delight for the customers’ craving for the best quality and durability. Their additives have time and again proved their mettle as the most efficient complement in our products.
DIVYA
TRIVAM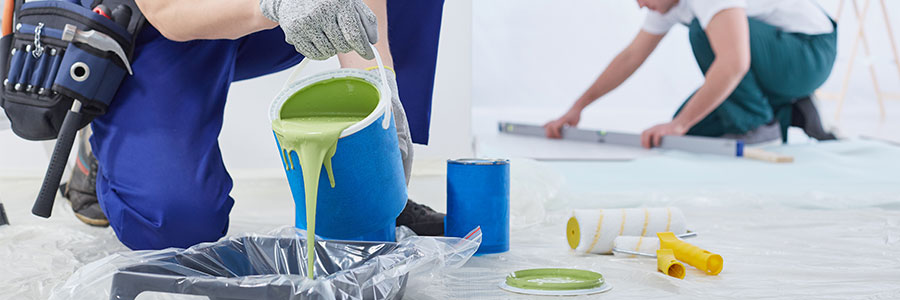
The water addition is one of the essential processes in the manufacturing of solvent based paints. The prime role of additives in this section is not only to give stability after water addition but to preserve the properties and functions of paint. Our best in the league experts ensure the right proportion of water addition in enabling to derive the best outcomes. Our recommendation and methods of usage for specific type of paints augur well for improved results after applying it.
The standard of materials produced by Raj Specialty Additives is simply one of the best in the industry of paints. The additives have enabled our final product to shimmer when put to rigorous trials of tests and has been hailed as the most potent under all circumstances.
RAMYA
TRIVAM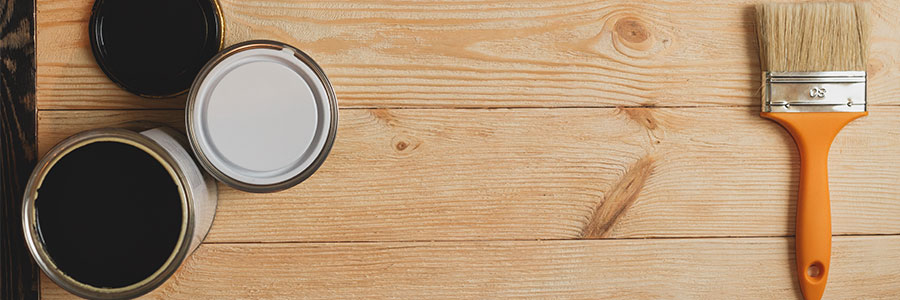
Defined as a class of additives which decisively calibrate the rheological attributes of liquid preparation, rheology modifiers are one of the most crucial aspects in the application of paints. Rheology modifiers predominantly find their utility to offer Thixotropic & newtonian viscosity properties.
The passion for innovation and technology in production continue to symbolize their entity – Raj Specialty Additives. Their ambitious products line of additives has enhanced the customer satisfaction of our products and it displays their finest of forte. The resolute quality of their additives has embodied the resplendent array of products manufactured at our facility.
REHNA
RIDIT
These agents are primarily used to offer stability in emulsions and offer their capability to produce dispersion solutions specifically for paint and in the distribution of pigment. Our guidelines for the agent provide the exact technology needed for stability and uniformity in the coatings.
Raj Specialty additives continue to gladden hearts with their wide range of offering of additives and it is an absolute delight for the customers’ craving for the best quality and durability. Their additives have time and again proved their mettle as the most efficient complement in our products.
RAJAN
POTJAMark DC 1310 is an Antisettling agent which goes beyond its expectations in delivering the desired results. And it is in concentrated form so the dosage is only 40% of its contemporary popular brands available in market.
Mr.Gunjan Pandya
Technical Manager, 20 Microns Ltd.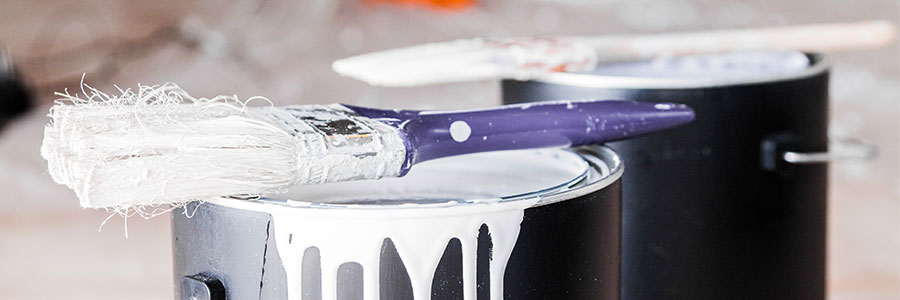
Defoamer, also invariably referred as an anti-foaming agent is actually a chemical additive and is widely preferred for its inherent characteristic to drastically minimize and hamper foam formation in liquids produced out of complex industrial process. Our methodology of use for different types of systems needs to be adhered properly for effective results.
The standard of materials produced by Raj Specialty Additives is simply one of the best in the industry of paints. The additives have enabled our final product to shimmer when put to rigorous trials of tests and has been hailed as the most potent under all circumstances.
DIYA
RAIZ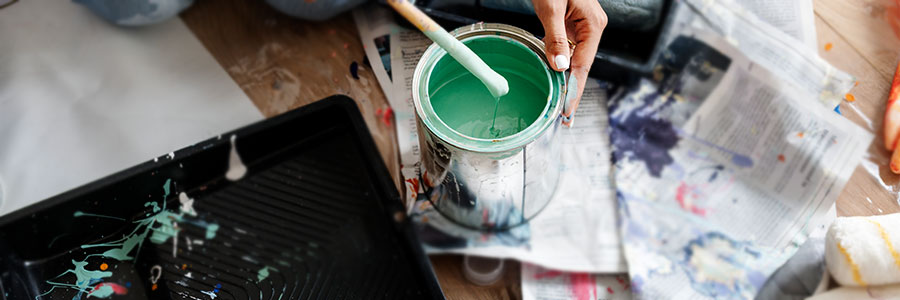
As specified by its terminology, multifunctional additives find their purpose in a range of requirements to reduce the problems associated with use of multiple chemicals and additives like errors by labour, wastage, ease in process & inventory maintenance headaches. Depending on the medium of application, the recommendations on the usage of these additives vary accordingly. The percentage of mixing has to be exactly complied with for various types of paints.
The passion for innovation and technology in production continue to symbolize their entity – Raj Specialty Additives. Their ambitious products line of additives has enhanced the customer satisfaction of our products and it displays their finest of forte. The resolute quality of their additives has embodied the resplendent array of products manufactured at our facility.
REEMA
DITRI
These agents are mainly used to modify the paint drying properties as required to slow or hasten.
Raj Specialty additives continue to gladden hearts with their wide range of offering of additives and it is an absolute delight for the customers’ craving for the best quality and durability. Their additives have time and again proved their mettle as the most efficient complement in our products.
RIDUTH
VANTEC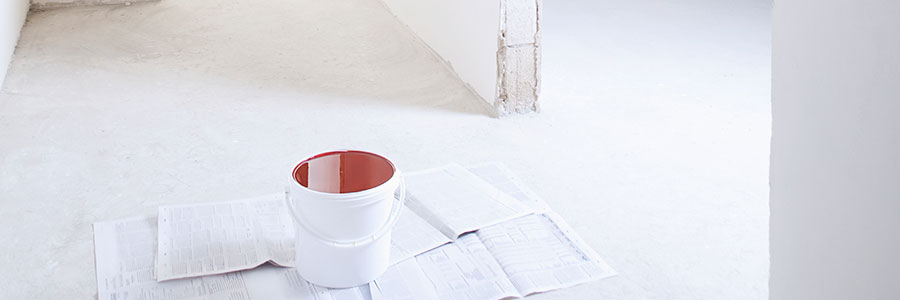
These additives are used to impart specific surface properties to coating systems as required. They can improve gloss or improve slip & mar resistance properties or enhance the flow & leveling properties, Water & dust repellency too.
The standard of materials produced by Raj Specialty Additives is simply one of the best in the industry of paints. The additives have enabled our final product to shimmer when put to rigorous trials of tests and has been hailed as the most potent under all circumstances.
RAM
TRIDENT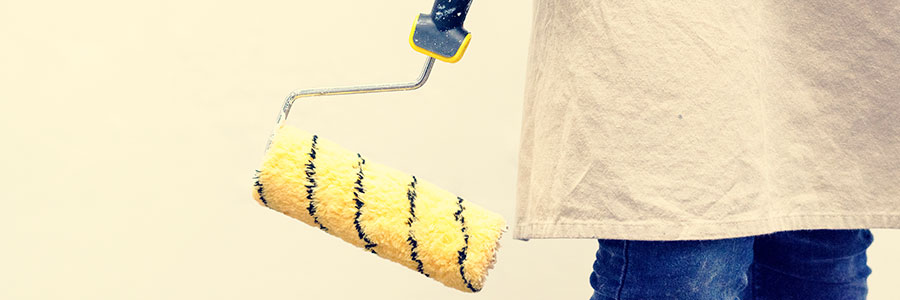
The important features is to influence the pH of the system as desired. For better optimization the dosage needs to be measured with respect to the type of system. The concentration proportion also has to be duly followed based on the standard set of procedures.
The passion for innovation and technology in production continue to symbolize their entity – Raj Specialty Additives. Their ambitious products line of additives has enhanced the customer satisfaction of our products and it displays their finest of forte. The resolute quality of their additives has embodied the resplendent array of products manufactured at our facility.
REMO
DITIRAs far as long term pH stability of paint is concerned, MARK DC 1810 ensures that the issues related to paint performance due to pH change on storage are totally prevented.
Mr.Gunjan Pandya
Technical Manager, 20 Microns Ltd.INDUSTRIES
PRODUCTS
CLIENTS
ACCOLADES
WHAT PEOPLE SAID
THEY HAPPY WITH US
The passion for innovation and technology in production continue to symbolize their entity – Raj Specialty Additives. Their ambitious products line of additives has enhanced the customer satisfaction of our products and it displays their finest of forte. The resolute quality of their additives has embodied the resplendent array of products manufactured at our facility.
RAJAN
DIGITECH